Percetakan tiga dimensi (
3D printing) tidak sebaru yang anda kira! Pada tahun 2009 ketika paten untuk
Fused Deposition Modeling (
FDM) kedaluwarsa, percetakan tiga dimensi menjadi sebuah topik hangat yang mudah untuk meyakini bahwa hal itu adalah sebuah merek inovasi baru. Dan karena mendapat liputan dari media secara luas, orang-orang sering membayangkan bahwa FDM teknik manufaktur tambahan. Nyatanya, teknik percetakan tiga dimensi pertama adalah SLA (
Stereolithography), bukan FDM, dan paten pertama diajukan di awal tahun 1980an! Penasaran? Ini adalah
timeline singkat sejarah dari percetakan tiga dimensi, dimulai dari 1980an sampai saat ini, dari mesin-mesin pertama hingga harapan-harapan besar dan banyak aplikasi yang sedang berkembang pesat saat ini.
Tahun 1980an: Kelahiran dari tiga teknik percetakan tiga dimensi.
Upaya percetakan tiga dimensi pertama kali dilakukan oleh Dr Kodama ketika mengembangkan sebuah teknik prototype yang cepat di tahun 1980. Dia yang pertama menjelaskan pendekatan lapisan per lapisan pada proses manufaktur, membuat sebuah cikal bakal dari teknik SLA, yaitu sebuah resin
photosensitive yang dipolimerisasi dengan cahaya ultraviolet. Sayangnya, dia tidak mengajukan persyaratan untuk paten sebelum
deadline.
Empat tahun kemudian, sekelompok insinyur berkebangsaan Perancis tertarik dengan
Stereolithography, tetapi ditinggalkan karena secara perspektif bisnis dinilai kurang.
Di saat yang sama, Charles Hull juga tertarik dengan teknologi tersebut dan dia mematenkan
Stereolithography pada tahun 1986.
Dia mendirikan 3D System Corporation dan setahun kemudian menghasilkan SLA-1.
Pada tahun 1988, di University of Texas, Carl Deckard membawa sebuah paten untuk teknologi SLS, sebuah teknik percetakan tiga dimensi yang lain yaitu dengan menggabungkan secara lokal bubuk gandum dengan sinar laser.
Sementara itu, Scott Crump, salah satu pendiri dari Stratasys Inc. mengajukan sebuah paten untuk
Fused Deposition Modelling (FDM): teknik ketiga dari teknologi utama percetakan tiga dimensi yang selama kurang dari sepuluh tahun, ketiga teknik utama dari percetakan tiga dimensi telah dipatenkan dan percetakan tiga dimensi telah lahir!
Gambar Mesin SLA-1
1980 : paten pertama oleh Dr Kodama untuk teknologi
Rapid prototyping.
1984 :
Stereolithography ditinggalkan oleh insinyur Perancis.
1986 :
Stereolithography dipatenkan oleh Charles Hull.
1987 : mesin pertama SLA-1.
1988 : mesin pertama SLS oleh DTM Inc. yang kemudian membeli sistem tiga dimensi.
Tahun 1990an: Kemunculan Manufaktur utama dari percetakan tiga dimensi dan alat-alat CAD.
Di Eropa, EOS GmbH didirikan dan membuat sistem EOS “Stereos“ pertama kalinya untuk industri prototyping dan aplikasi produksi di percetakan tiga dimensi. Kualitas industri ini dikenal luas pada teknologi SLS untuk plastik dan logam.
Di tahun 1992, paten FDM dikeluarkan oleh Stratasys, yang mengembangkan printer tiga dimensi untuk profesional maupun individu.
Mulai dari tahun 1993 hingga 1994, pemain utama dari percetakan tiga dimensi, berkembang dengan bermacam-macam teknik:
- ZCorp dan binder jetting: dengan menggunakan teknologi inkjet percetakan yang dibuat oleh MIT, ZCorp menciptakan Z402 yang memproduksi model menggunakan material berbahan dasar serbuk/plaster dan binder cair yang berbahan dasar air.
- Teknologi Arcam MCP dan Selective Laser Melting.
Di saat yang sama, alat-alat CAD
(Computer Aided Design) untuk cetak tiga dimensi semakin banyak tersedia dan berkembang. Sebagai contoh, pembuatan cetak biru Sanders (sekarang dikenal sebagai Solidscape), salah satu yang mengembangkan alat-alat yang khusus untuk tambahan manufaktur.
Di tahun 1990an yang juga dekade dari aplikasi pertama percetakan tiga dimensi dilakukan oleh peneliti di bidang medis yang mengkombinasikan dunia medis dan percetakan tiga dimensi sehingga membuka jalan untuk kegunaan yang lainnya.
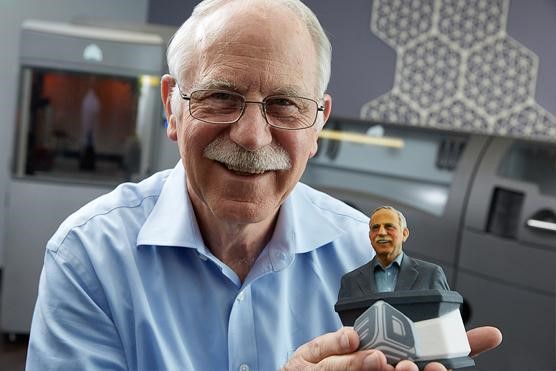
Charles Hull
Ikhtisar:
1990 : sistem EOS Stereos pertama.
1992 : paten FDM oleh Stratasys.
1993 : Solidscape didirikan.
1995 : Zcorp mendapatkan lisensi khusus dari MIT.
1999 : organ buatan ditemukan dan membawa sesuatu yang canggih di bidang medis.
Tahun 2000an: percetakan tiga dimensi mendapat sorotan media.
Di tahun 2000, pertama kalinya percetakan tiga dimensi mencetak ginjal. Kita harus menunggu tiga belas tahun lebih untuk melihat ginjal tersebut ditransplantasikan ke pasien. Ginjal cetak tiga dimensi saat ini bekerja secara sempurna dan para peneliti sedang bereksperimen untuk mempercepat pertumbuhan dari organ transplantasi dengan sangat cepat.
Tahun 2004 adalah tahun inisialisasi dari
RepRap Project yang terdiri sebuah printer tiga dimensi yang dapat mereplikasi sendiri. Proyek
open source in memimpin penyebaran dari komputer tiga dimensi berbasis FDM, printer tiga dimensi dan popularitas teknologi di komunitas pembuat.
Tahun 2005, ZCorp meluncurkan Spectrum Z510, printer warna tiga dimensi
high-definition paling pertama.
Di tahun 2008, percetakan tiga dimensi mendapat ucapan terima kasih yang lebih besar dari media untuk aplikasi media lainnya yaitu kaki, printer tiga dimensi berhasil mencetak kaki palsu. Proses pencetakan kaki palsu tersebut, menggabungkan semua bagian dari sebuah kaki, yang dicetak seperti apa adanya tanpa membutuhkan tambahan perakitan.
Sekarang ini, dikombinasikan dengan pemindaian tiga dimensi, prostesis dan ortosis lebih murah dan sangat cepat untuk diperoleh.
Tahun 2009 adalah tahun ketika paten FDM jatuh ke publik, sehingga membuka jalan untuk gelombang inovasi pada printer tiga dimensi berbasis FDM, menurunkan harga komputer cetak tiga dimensi dan konsekuensinya karna teknologinya semakin mudah diakses, membuat teknologi percetakan tiga dimensi semakin mudah dilihat.
Tahun 2009 juga tahun Sculpteo diciptakan, salah satu pionir dari jasa percetakan tiga dimensi
online yang berkembang cepat saat ini, yang merupakan langkah maju dari akses percetakan tiga dimensi.
Ikthisar:
2000 : sebuah ginjal cetak tiga dimensi diciptakan.
2000 : MCP Technologies memperkenalkan teknologi SLM.
2005 : ZCorp meluncurkan Spectrum Z510 yang merupakan printer warna tiga dimensi
high-definition di pasaran.
2006 : sebuah proyek
open source diinisalisasi oleh Reprap.
2008 : kaki buatan dicetak secara tiga dimensi pertama kali.
2009 : paten FDM menjadi domain publik.
2009 : Sculpteo diciptakan.
Tahun 2010an: Tahun visibilitas, inovasi dan harapan untuk percetakan tiga dimensi.
Tahun belakangan ini menjadi sesuatu yang sangat penting untuk percetakan tiga dimensi. Dengan kadaluarsanya paten FDM, tahun pertama dari dekade ini menjadi tahunnya percetakan tiga dimensi. Teknologi komputer menyerbu pasaran dan membuat sektor industri berpikir kembali untuk manufaktur tambahan sebagai sebuah teknik produksi yang andal. Di tahun 2013, presiden Amerika Serikat Barack Obama menyebut bahwa percetakan tiga dimensi sebagai isu utama untuk masa depan pada pidato
State of the Union-nya yang membuat “3D printing” menjadi sebuah kata kunci.
Tahun 2010, Urbee adalah mobil
prototype yang dicetak secara tiga dimensi pertama kalinya. Badannya utuh dan dicetak tiga dimensi dengan menggunakan printer tiga dimensi yang sangat besar. Saat ini, mobil cetak tiga dimensi masih sebuah impian dibanding kenyataan tetapi pada proses manufaktur, banyak pemain mempertimbangkan hal itu sebagai alternatif yang baik dari metode tradisional.
Di 2011, Cornell University mulai membangun sebuah printer makanan tiga dimensi. Sekilas, tampak tidak berarti apa-apa, namun NASA untuk saat ini sedang meneliti bagaimana printer tiga dimensi mencetak makanan di luar angkasa.
Tahun 2014, NASA membawa sebuah printer tiga dimensi ke luar angkasa untuk membuat objek cetakan tiga dimensi ke luar bumi.
Banyak hal canggih di bidang medis percetakan tiga dimensi: jaringan, organ tubuh, dan prostesis berbiaya murah.
Printer tiga dimensi diberitakan secara teratur, bahwa alat tersebut lebih efisien, mencetak lebih cepat, memberi akses untuk bahan-bahan tiga dimensi yang baru. Sebagai contoh yang baik, teknologi dari Carbon 3D CLIP, yang kita tawarkan sebuah layanan pada
platform sejak Maret 2016 dan printer tiga dimensi ini mencetak resin mekanik dengan kecepatan yang tidak ada bandingnya.
Bahan percetakan tiga dimensi yang baru dieksplor setiap hari, mulai dari percetakan tulang oleh laboratorium Daniel Kelly’s hingga
startup asal Perancis XtreeE yang membuat percetakan beton tiga dimensi yang merevolusi industri kostruksi!
Di saat yang sama, upaya yang secara konstan dibuat untuk menjadikan percetakan tiga dimensi lebih dapat diakses lagi, melalui pendidikan,
shared spaces seperti
fablabs and makerspaces dan juga layanan percetakan tiga dimensi seperti yang dilakukan oleh
Sculpteo.
Ikhtisar:
2010 : Urbee adalah mobil prototype yang dicetak secara tiga dimensi pertama yang ditampilkan.
2011 : Cornell University memulai membangun printer makanan tiga dimensi.
2012 : rahang buatan pertama dicetak dan diimplankan.
2013 : ”3D printing” di pidato
State of the Union Obama.
2015 :
Carbon 3D mengeluarkan mesin cetak revolusioner mereka ultra-fast CLIP 3D.
2016 : laboratorium Daniel Kelly mengumumkan bahwa mereka dapat mencetak tulang secara tiga dimensi.
sumber:
https://www.sculpteo.com/blog/2016/12/14/the-history-of-3d-printing-3d-printing-technologies-from-the-80s-to-today/